- Automatically improving Dynamic Recipes prescribe settings for the best production runs under varying conditions
- Productivity KPI Model lets manufacturers optimize production according to their own preferred metrics
SAN FRANCISCO, Oct. 20, 2020—Sight Machine Inc. today announced groundbreaking enhancements to its manufacturing productivity platform that put Industry 4.0’s promise of the smart factory within reach of manufacturers.
New Dynamic Recipes continuously and automatically update prescribed production settings, searching through the entire available production history to identify the settings that lead to the best results. They capture the optimal machine settings for every combination of conditions encountered, including the type of raw materials and environmental conditions, as well as for different types of output (e.g., grades of paper).
Sight Machine has also introduced a new Productivity KPI Model that lets manufacturers optimize production according to their own preferred metrics. These metrics vary widely among companies, but typically include quality, uptime and throughput, which together comprise Overall Equipment Effectiveness (OEE). Productivity KPIs give manufacturers consistent, apples-to-apples metrics to track productivity of all lines and plants across the enterprise.

Dynamic Recipes optimize for any combination of targeted Productivity KPIs, such as minimizing cost and maximizing throughput. The prescribed recommendations automatically adjust as conditions change, and recipes automatically improve to reflect new top-performing production runs.
“Through eight years of continuous improvement of our platform, we have reached the threshold of enabling true Smart Manufacturing, giving manufacturers automated continuous improvement of processes and the ability to manage all production assets using a common yardstick,” said Sight Machine CEO and Co-Founder Jon Sobel. “For the first time, manufacturers are truly able to track the performance of all their machines, lines and plants, using a uniform metric: how well is this asset performing versus its maximum potential performance?”
Sight Machine is the only company able to deliver these capabilities in real-world manufacturing environments due to two fundamental elements of its platform. First is the platform’s unique data modeling foundation. Sight Machine takes the dozens of incompatible data types generated by factory equipment and manufacturing software and generates a digital representation of the entire production process, including processes, production lines, downtime and defects.

Second, the product continuously models and analyzes all production data in real time, allowing manufacturers to monitor and improve current performance instead of only analyzing past performance.
Sight Machine’s unique foundation enables it to analyze and optimize multi-stage manufacturing processes like paper- and glass-making, where output quality may be measurable only hours or days after a defect is caused. Sight Machine connects the quality results of a finished product or batch with the conditions and machine settings during each stage of that batch being manufactured, identifying the cause of the quality defect and prescribing the settings that will reduce defect frequency.
From Descriptive to Prescriptive Analytics
Previous generations of the Sight Machine platform have been used primarily to help manufacturers understand how their factories are doing and analyze how to improve them, using a large toolset of descriptive analytics. The new enhancements go beyond descriptive analytics to meet an even harder challenge: providing robust and reliable prescriptive analytics, proactively recommending the settings and processes needed to achieve the highest productivity under ever-changing conditions.
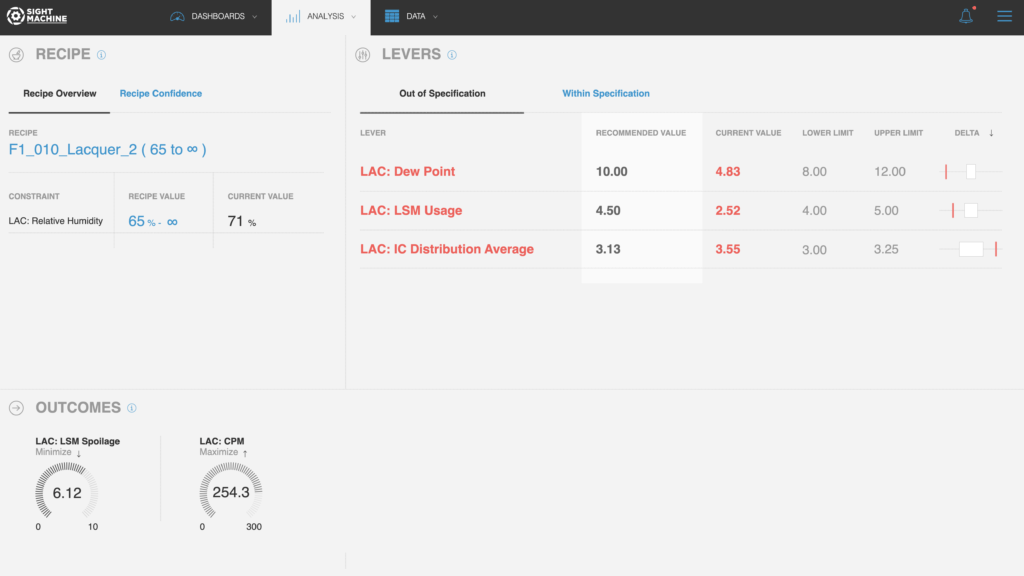
Operators in the control room or on the plant floor interact with Dynamic Recipes using a new application called Operator Co-Pilot. The application automatically detects current conditions (e.g. raw materials, desired output grade, humidity) and provides recommended machine settings to optimize for the desired outcomes.
“These new capabilities help manufacturers be on their toes rather than on their heels, preventing problems from happening in the first place rather than trying to solve problems that have already occurred,” said Andrew Home, Sight Machine’s VP of Product.
About Sight Machine
Sight Machine drives rapid increases in manufacturing productivity. Our manufacturing productivity platform delivers real outcomes in efficiency, sustainability and quality. Manufacturers that deploy Sight Machine’s software empower teams to better collaborate, innovate and accelerate their journey of continuous productivity improvement. Founded by a team with deep manufacturing expertise, Sight Machine has offices in San Francisco and Ann Arbor, Mich. (www.sightmachine.com).
Sight Machine media contact:
Media@sightmachine.com